Choosing the Right Defoamer for Your Particular Application Demands
Picking the suitable defoamer for particular application demands is a nuanced process that requires mindful consideration of several factors, such as the foam operating, medium, and kind conditions. Understanding the subtleties of defoamer efficiency-- including speed and perseverance-- while likewise representing regulative and environmental variables is important. Furthermore, engaging in trials and seeking advice from makers can give valuable understandings. However, browsing these intricacies can be challenging, and the consequences of a bad selection might be significant. What approaches can be used to make sure an ideal selection?
Understanding Foam Formation
Foam formation occurs when gas is caught within a liquid, creating a stable framework of bubbles. This sensation can considerably affect different industrial procedures, particularly in industries such as food production, pharmaceuticals, and wastewater therapy. The visibility of foam can hinder mixing, decrease product quality, and even lead to functional inadequacies.
Foam typically forms as a result of a mix of factors, including surface-active representatives, frustration, and the features of the liquid phase. Surfactants lower the surface area tension of the liquid, helping with the development of bubbles that can integrate and support. Agitation, whether from mechanical stirring or gas intro, enhances bubble development, resulting in raised foam volume.
Recognizing the mechanics of foam formation is crucial for industries intending to optimize their processes. By recognizing the particular conditions that advertise foam generation, companies can implement strategies to alleviate its impacts.
Kinds Of Defoamers Available
Different sorts of defoamers are available to deal with the challenges presented by foam in commercial applications. defoamers. Extensively classified, defoamers come under three groups: silicone-based, non-silicone-based, and natural defoamers
Silicone-based defoamers are renowned for their efficiency and security across a large range of temperature levels and pH levels. They are commonly used in applications where solid foam reductions is needed, such as in layers, adhesives, and paints. Their low surface tension allows for fast foam collapse.
Non-silicone-based defoamers, commonly made from natural substances, provide an alternative for applications conscious silicone residues. These defoamers can be additional divided right into polyether and ester kinds, each customized to satisfy particular solution requirements. Non-silicone defoamers are frequently utilized in food handling and personal treatment items as a result of their compatibility with numerous formulas.
Natural defoamers, stemmed from plant or pet sources, are gaining traction because of their environment-friendly profile. These items are specifically appealing in applications where governing conformity and sustainability are paramount, such as in agrochemicals and biotechnology.
Picking the right type of defoamer is vital for enhancing performance and guaranteeing compatibility with certain applications.
Secret Application Considerations
When selecting a defoamer, it is vital to think about the particular application requirements to ensure ideal efficiency. defoamers. Different industries have distinctive needs, such as food processing, drugs, or wastewater therapy, and each application may need special defoaming properties
Trick aspects to review consist of the medium in which the defoamer will certainly be utilized, whether it is water-based, oil-based, or a mix thereof. The temperature level and pH levels of the application can additionally considerably affect the performance of a defoamer. In addition, compatibility with various other chemicals existing in the system is crucial to avoid negative responses that might endanger efficiency.
One more crucial factor to consider is the lathering behavior of the certain system. Comprehending whether the foam forms swiftly or slowly can guide the option of a defoamer that targets the root cause efficiently. The preferred rate of defoaming can influence the selection, as some applications call for rapid action while others might endure slower defoaming processes.
Finally, governing and environmental factors to consider ought to not be forgotten, especially in sectors with strict compliance demands. Selecting a defoamer that straightens with these factors guarantees both effectiveness and security in the application.
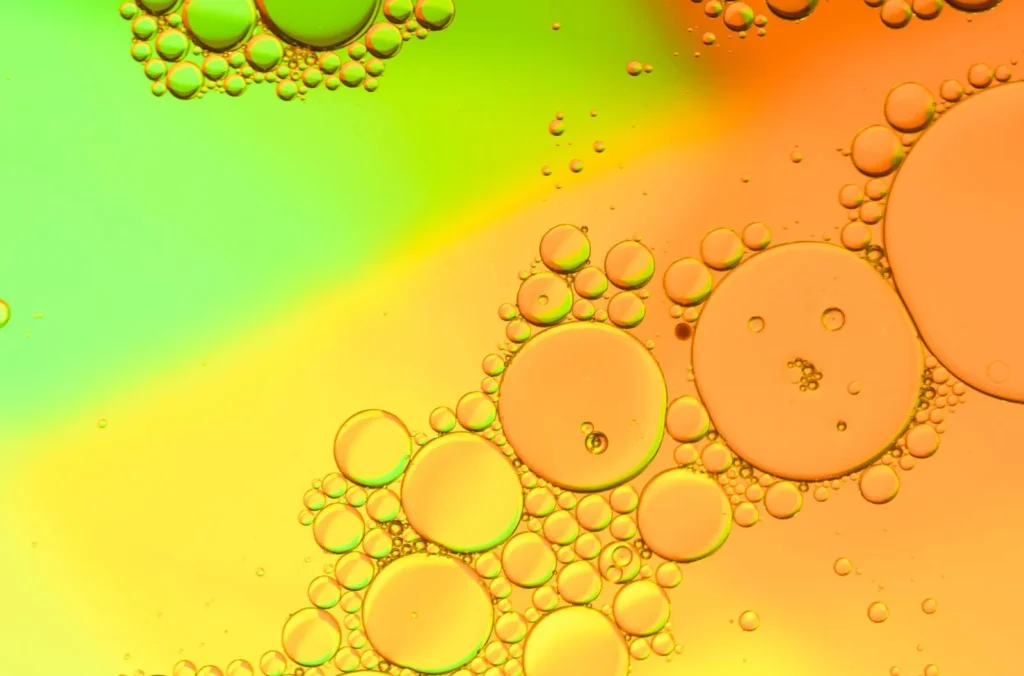
Performance Testing Techniques
Examining the performance of a defoamer requires a methodical method to testing that properly determines its performance in certain applications. Different performance screening techniques can be utilized to ascertain the optimum defoamer for a provided formula.
One typical method is the bubble examination, which assesses the defoamer's capacity to lower foam volume gradually. This test entails producing a secure foam and after that including the defoamer to observe the rate of foam collapse. Another method is the dynamic foam examination, where foam is created under regulated conditions to imitate real-world application scenarios. This strategy offers insights right into exactly how the defoamer performs under varying shear conditions.
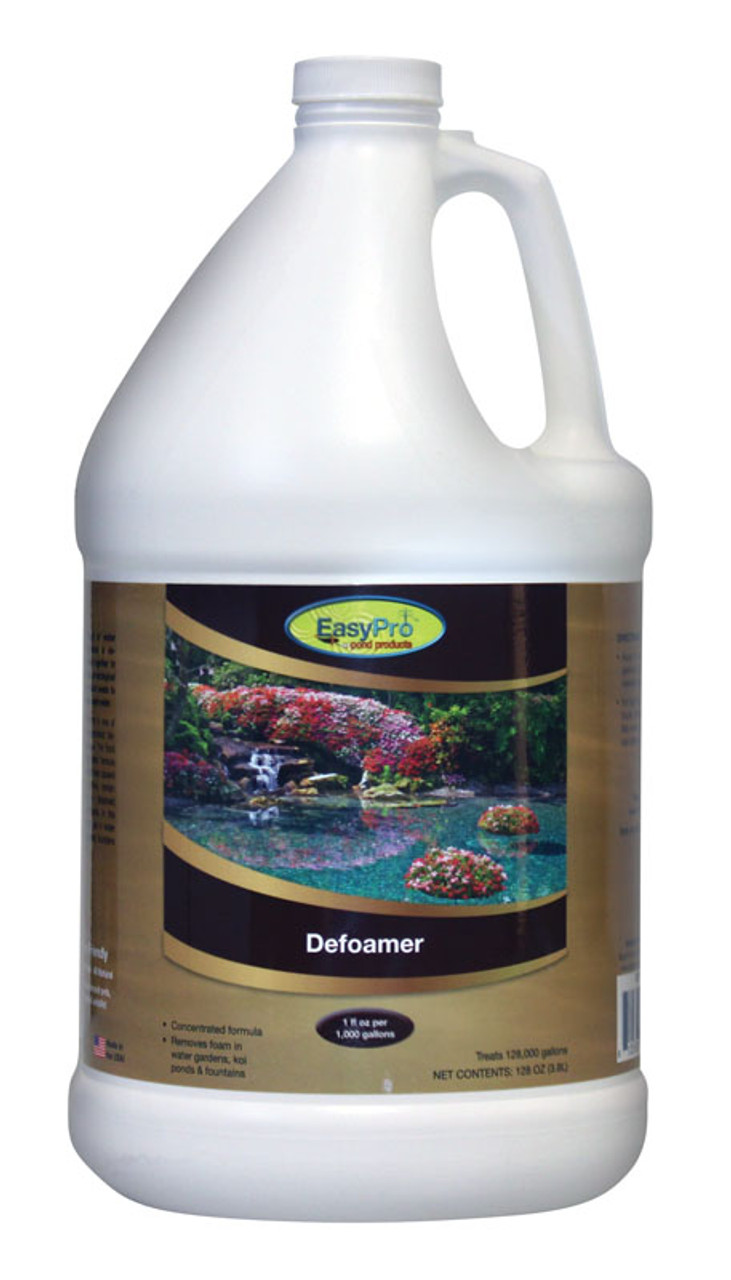
Ultimately, selecting the suitable performance testing technique depends upon the certain application and the kind of foam being resolved. Each technique supplies beneficial information that can lead formula changes and boost the performance of the defoamer in sensible applications.
Ideal Practices for Selection


Following, consider the defoamer's efficiency in regards to speed of action and perseverance. A quick-acting defoamer might be needed for procedures where rapid foam reductions is vital, while a more persistent solution may be needed for prolonged foam control. In addition, evaluate the environmental effect of the defoamer, including its biodegradability and any type of governing compliance needs.
Conduct tests with picked defoamers to determine their performance in real-world conditions. This step is crucial to validate that the chosen item satisfies performance assumptions. Seek advice from with manufacturers or distributors for technological support and guidance, as they can provide valuable insights right into item formulas and application strategies. By sticking to these best practices, you can improve foam control efficiency and make sure the long life of your processes.
Final Thought
In summary, picking the suitable defoamer demands a thorough assessment of numerous look at this site factors, consisting of foam kind, tool, operating problems, and ecological considerations. Understanding the special attributes of foam development and the readily available defoamer alternatives is vital. In addition, using efficient efficiency screening techniques and sticking to finest techniques during the choice process will certainly improve the possibility of accomplishing optimal defoaming results. Inevitably, an educated option strategy will address details application demands and minimize foaming difficulties efficiently.
Selecting the website link proper defoamer for certain application demands is a nuanced procedure that requires careful factor to consider of numerous variables, such as the foam operating, tool, and type problems.Selecting the right defoamer is important for attaining optimum efficiency in foam control applications. A quick-acting defoamer might be required for processes where quick foam reductions is critical, while an extra persistent formulation may be required for prolonged foam control.In summary, choosing the ideal defoamer demands a thorough evaluation of various variables, consisting of foam type, tool, operating problems, and ecological considerations. Recognizing the special characteristics of foam formation and the readily available defoamer choices is important.